Several textile manufacturers have started to integrate light optical fiber into their textiles naturally. If the first tests were successful on clothing, the first bright textiles were produced for interior fittings, hotel decoration or for marketing at points of sale.
Since then, these luminous fabrics have developed for a number of uses far removed from the "designer and decorative luminous fabric", particularly in the medical field. Today there are several medical applications such as the treatment of jaundice in infants or the treatment against pre-cancerous skin bonds which require the use of a luminous tissue in a particular wavelength.
Implementation of luminous optical fiber weaving
Weaving approach
This weaving can be done from traditional weaving looms such as the Jacquard loom but also from yarn knitting machines(knitters) or even braiding machines to make cords.
The light effect of the fiber is related to the surface of the fiber, the fiber density and the intensity of the light source.Thus a fiber of diameter 1mm will have a light effect 4 times more important than a fiber of diameter 0.5mm using the same light source
In the end, a bare fiber with a diameter of0.5mm represents a good compromise between light effect and flexibility forluminous textiles.
First rules to respect
The weaving process and the storage of thetextile must not damage the optical qualities of the fiber. In all these operations, abrasive materials and cutting parts can damage the fiber. Great attention will be paid to cleaning, transport, the pieces of fabric must bewell protected to avoid damage to the fiber.
Fiber density choice
The fiber density will depend on the type of use, making it possible to meet a requirement such as the power radiated on thesurface, on the contrary, is a cost constraint.
The higher the density of fibers for a given diameter, the more the power of electromagnetic radiation per unit area can be optimized. This quantity is called the irradiance and is expressed in W / m2;for a luminous fabric it is expressed in mW / cm2.
Furthermore, this density of fibers directly impacts the cost of the final solution. Indeed there is the price of fiber but it remains almost marginal versus the cost of mounting connectors and the implementation of light sources. The number of collectors and light sources isdirectly correlated to the fiber diameter and their fiber density per cm2.
In a medical use such as for example the treatment of jaundice in infants or the treatment against pre-cancerous cutaneous connections, one must expose a part of the patient's body on aluminous tissue with a homogeneous diffusion of light over a length of specificwave over the entire surface. We will favor the density of fibers on luminous fabrics whose surfaces do not exceed a few tens of dm2 as shown by this luminous fabric for the treatment of actinic keratosis.
For a luminous textile for decorative purposes,the manufacturer will have to pay attention to the final cost. This will become all the more true for large areas larger than 1 m2. To decrease the density offibers without this being apparent, there are possible tricks.
The two photos below show that a fabric with a low density of optical fibers can have an interesting rendering whether it is lit or not. When not lit, optical fibers are not visible due to their low density.
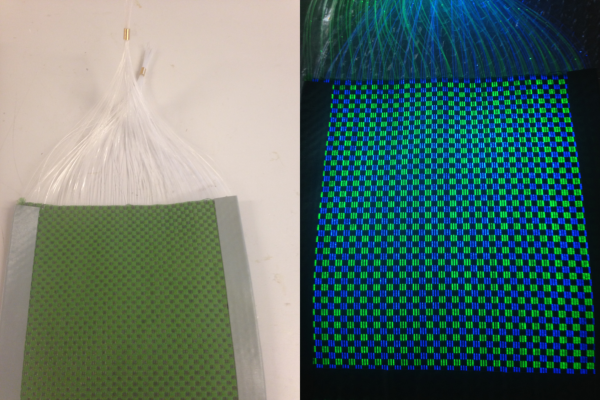
The other approach to reducing the quantity offibers is not to weave the whole of optical fiber but to select one or more repeating pattern (s). The attached photo shows a curtain with a repeated pattern made of bright optical fiber.
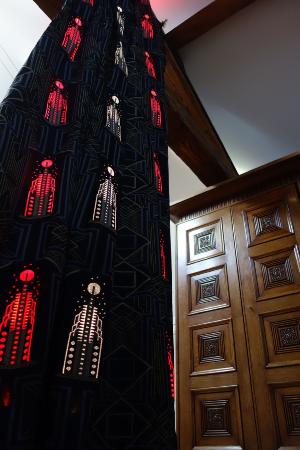
Fiber resistance
It is necessary that the weaving of the fibers is well held by threads without being too tight to avoid loss of light by playing on the radius of bending of the fiber.
The fibers on the invisible part must be stretched but must be attached by few threads.
Mounting of collectors
These fibers must be powered by light sources.To this end, the fibers are collected in a collector which will be connected to the output of the light source.
The work of assembling the collectors can become very tedious if certain rules are not respected.
The first rule is to find a trick to detach fibers very easily and then join them in the collector.
The second rule is to leave a certain length of fiber free to easily collect all the fibers in the collector. This length is at least equal to the width of the fibers next to each other plus the length of the collector.
Suppose we have to combine 75 fibers of 0.5mm dia in a 4cm collector, a calculation easily gives a minimum length of 9cm (4cm+ 5cm) taking into account the density of 15 fibers 0.5 dia per cm.